laser-cut & press-brake components
We manufacture complete machines out of laser-cut or press-brake manufactured parts:
- typical wall thickness of 1 - 5 mm, in comparison with classic welded parts with 5 - 100 mm thickness
- by reducing wall thickness we create lighter and less dear parts
- sheet metal can be laser-ed or cut classically
- when the parts are laser-cut, many further windows and cutouts can be realised without increasing cost
- laser-cut parts can then be bent or stamped on a press-brake, up to 6m length
- even larger parts have to be welded carefully, so that the work is invisible after painting
- our suppliers are equipped with modern Trumpf machines, so that the laser work and the bending can be made on the same machine
- large formats and strong thicknesses are manufactured on separate press-brakes
- when parts have only simple functions as a cover or a bracket, manufacturing is ending at this stage
- however, if strong and stiff parts are needed for machines, the parts usually have to be welded to form complete round or cubical structures
- of course different materials like steel and aluminium can also be joined, provided that welding is possible
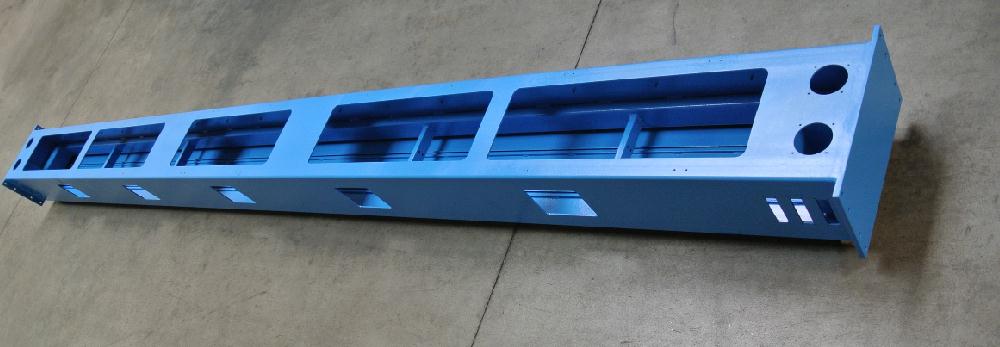
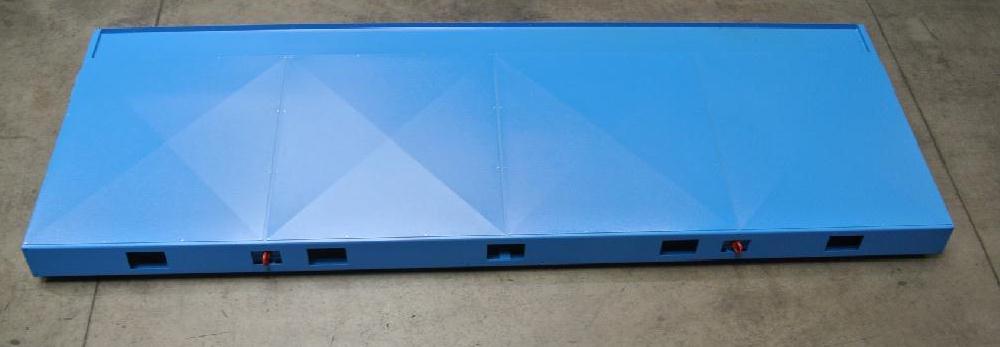
Further manufacturing steps can be:
- riveting or stamping of threaded rivets
- spot-welding of threaded bolts
- classical machining of course, but for direct cutting of threads the wall thickness usually is not strong enough
- painting the parts with wet paint or powder coating
- sealing the edges against water or air, before or after painting
- and of course assembly with further components, seals, etc.
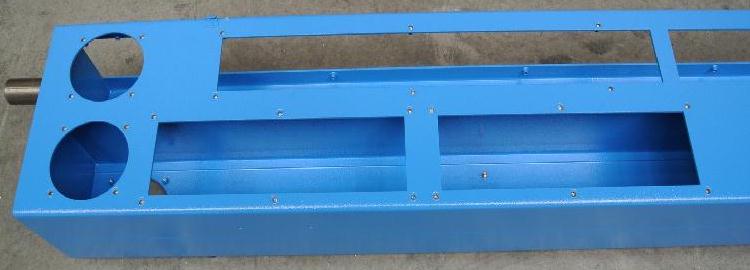
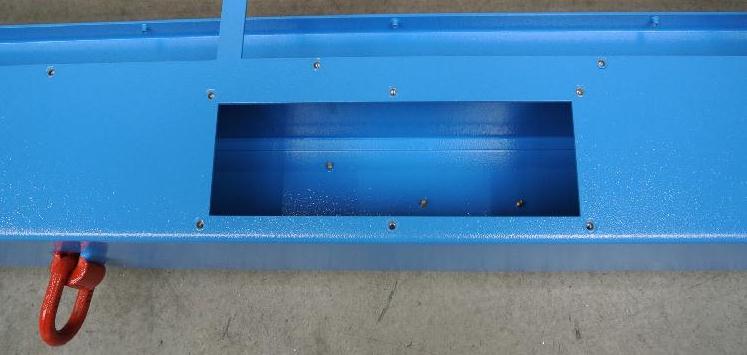
In comparison with classical welded components out of flame-cuts:
- due to the lower wall thickness the laser-cut parts are lighter, but of course not as stiff towards bending and shearing
- the expense for programming the laser and the press-brake is worthwhile for series parts, but not for individual components
- even though laser-cut parts are bent on the same machine automatically, there still remains a lot of manual work, especially if the sides have to be finally joined by welding
- welding seams often are potentially visible for the final customer and have to be carefully welded and polished
- theoretically laser-cut and bent parts form a parallel joint line, that has only to be welded
- however, practice shows that these parts first have to be straightened and clamped before welding, so that a high level of workmanship is necessary
- in order to produce beautiful welds on these parts, sometimes even longer than 6m, not many experts are available; standard craftsmen are not all alike
- it is financially not interesting to replace standard stock profiles by laser-cut parts
- however, when the laser-cut parts are well designed and manufactured, they achieve a certain "lightness", that adds to the good design of the total machine and that is also honoured by the final customer
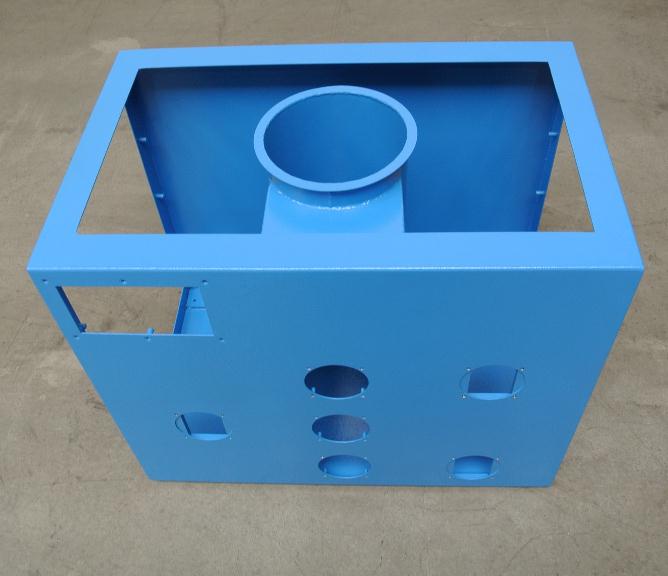
We can manufacture parts and components for machinery by 3 different technologies:
- as castings
- as welded parts out of flame-cuts, typically 5 - 100 mm thick
- as laser-cut or press-brake parts, typically 1 - 5 mm thick